Model NO.: BOSJ-S
Customized: Customized
Advantage: Easy to Maintenance
Condition: New
Usage: Multifunctional
Material of Roller: Gcr 15
Control System: PLC Control System
Processing Methods: Heat Treatment
Trademark: BOSJ
Transport Package: Wooden Cases
Origin: Jiangsu China
HS Code: 8455212000
WHY NOT PIPE CULVERT?
POPULAR OPINION DOESN'T MAKE IT RIGHT.
There is a popular school of thinking surrounding the question of round shelters vs square shelters.  There is no shortage of people and even "professionals" that will claim that a round shelter offers more strength than a square shelters. This couldn't be further from the truth.  It's easy to trace the origins of this pop-culture thinking back to the Roman arch style of  engineering.  At the time - this style of architecture was cutting edge and far stronger than anything else.  However; just as time has progressed bringing new ideas and technology; so in like fashion has our understanding of engineering grown.  Round is NOT stronger than everything else.Â
Working craft
Manual feeding----roll forming---Output
Operation area:20X 5.0 X 8(length X width X height)m
The direction of feeding: from left to right
 Power: 380V, 50Hz, 3 parch
Total Power:about 110k
 Main technical dat
Width of material sheet:1145Â mm
Thickness of material sheet:0.9-3.0mm
Low carbon steel,galvanized sheet,cold steel,etc
Working piece length:≤6000 mm    Â
This roll forming machine can produce the forming part of corrugated steel.
Product:Corrugated steel
General structure of equipment
Roll Forming Machine
Structure
 Cast steel+gearbox driven
Functions and Structure
After 20 roller stations,the profile is finished.It consists of DC motor,reducer motor,driven gearbox and rollers.Lathee Bed and drive box adopts welded structure and stress treatment; Gear takes 45 steel hard tooth surface.
Working piece length:≤6000 mm    Â
This roll forming machine can produce the forming part of corrugated steel.
Product:Corrugated steel
General structure of equipment
Roll Forming Machine
Structure
 Cast steel+gearbox driven
Functions and Structure
After 20 roller stations,the profile is finished.It consists of DC motor,reducer motor,driven gearbox and rollers.Lathee Bed and drive box adopts welded structure and stress treatment; Gear takes 45 steel hard tooth surface.
The roller uses the combinated structure, the speed difference and the forming resistance are small, the steel plate surface will be less wear; and also guaranteed the precision shape of the working piece with no scratch .The material of the roller is the GCr15 forging, after whole quenching then by numerical control processing, degree of hardness can reach HRC58-62; Has the characteristic with high strength, hardness, precision and long service life etc.
Driven type:it takes gearbox driven
Main technical parameters
NO. |
Items |
Unit |
Parameters |
Remarks |
 1 |
Material |
Type |
 |
Low carbon steel,Galvanized steel,etc |
 |
Tensile strength |
Map |
≥450 |
 |
Thickness |
mm |
1.2~4.2 |
 |
2 |
Specification |
mm |
       See pic. |
 |
3 |
Production speed |
m/min |
4 |
 |
4 |
Roller material |
 |
GCr15 Quenching treatment |
 |
5 |
Drive type |
 |
Gearbox |
 |
6 |
Motor power |
kw |
About 152 |
 |
7 |
Electric control system |
 |
PLCÂ frequenvy motor |
 |
8 |
Dimension(Length*Width*Height) |
m |
40X5X3.9 |
 |
Forming station: about 20stations
   Power of motor: 55X2=110kw frequency motor
Roller axis:¢280mm
Max feeding width:1145mm
Forming mould: one set
Full line is controlled by PLC control system with touch screen operation to achieve the human and PLC interactive. The operator can monitor the setting program (programmable control) and modify the parameter to control the line. Also can check the running status, parameter and error indication etc..
  Operation type: manual /auto two type switch. In manual position: can run the each part of the machine. In auto position: can run the full line. The emergency stop ensures the safe of the equipment and operator.
Â
Investment casting technical flow process
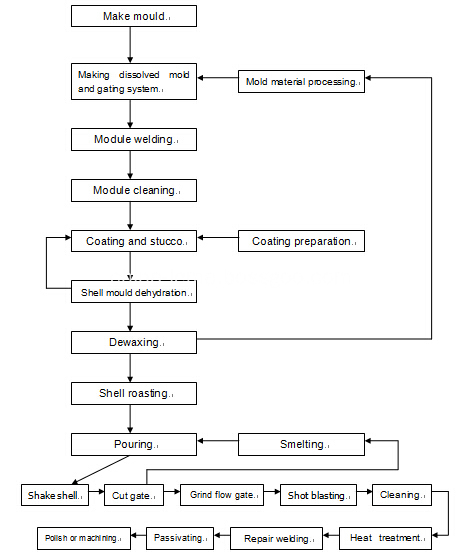
The silica sol casting process also called precision
investment casting process. It is a less cutting or no cutting casting
process. It is an excellent technique in foundry
industry. Its application is very extensive. It not only applicable to various
types, various kinds of alloy and casting, and produce the casting dimension
accuracy and surface quality is higher than other casting method, Even other
casting method can not do the complex, high temperature resistant, not easy
machining castings, all can be used for investment precision casting process.
The investment casting process, it is a process that use fusible
materials make soluble model, and coated with several layers of tailor-made
refractory coating on the surface, after drying and hardening become a whole
shell, melt the shell model by steam or hot water. Then put the shells in the
sand, filling dry sand in all round and modeling. Finally roasting it based on
high-temperature in the furnace, the shell after roasting, and getting the
casting part after pouring molten metal.
The investment casting process can produce High precision
dimensional parts, generally can reach to CT4-6(sand casting is CT10-13, die
casting is CT5-7). Due to the complexity of investment casting process, there
are many factors influencing the casting dimension accuracy. Such as shrinkage
of mold material, deformation of the casting, Shell heating and cooling line
quantity change in the process, alloy shrinkage and deformation of castings in
the solidification process. The surface finish of investment castings is higher
than the ordinary casting, can reach to Ra1.6~3.2.
The greatest advantages of investment casting is casting parts
have high dimensional accuracy and surface finish, so it can reduce the
mechanical processing. The another advantage of investment casting method is
that it can cast all kinds of alloy and complex casting part, special casting
high temperature alloy casting part.
The precision of the Steel Casting Part: ±0.15mm~
Smoothness of surface of rough part: Ra6.4;
Shrinkage rate of steel investment casting products: 0.6%;
Material wastage rate: 5%;
General stainless steel casting part machining allowance: 0.7mm;
Surface preparation methods: Sand blasted, Shot blasting, Powder coating,
Painting, Plating, Electrophoresis, Polishing.
Our
company's production equipment and management system
CNC machining center: 8 sets AIGEMA A-8;
CNC lathe machine: 6 Guangzhou Machines and 7 Shenyang Machines;
Work days of one week: From Monday to Saturday;
Shift work: 2 shift per day;
Working hours: From AM 8:00 to PM 5:00;
2D and 3D drawing Software: AutoCAD, UG, Pro/E, SolidWorks 2013;
QC control: New type NANO CMM, FPI M5000 desktop metal analyzer, Easson
projector, Mechanical properties tester.
The steel casting process and machining
equipment:
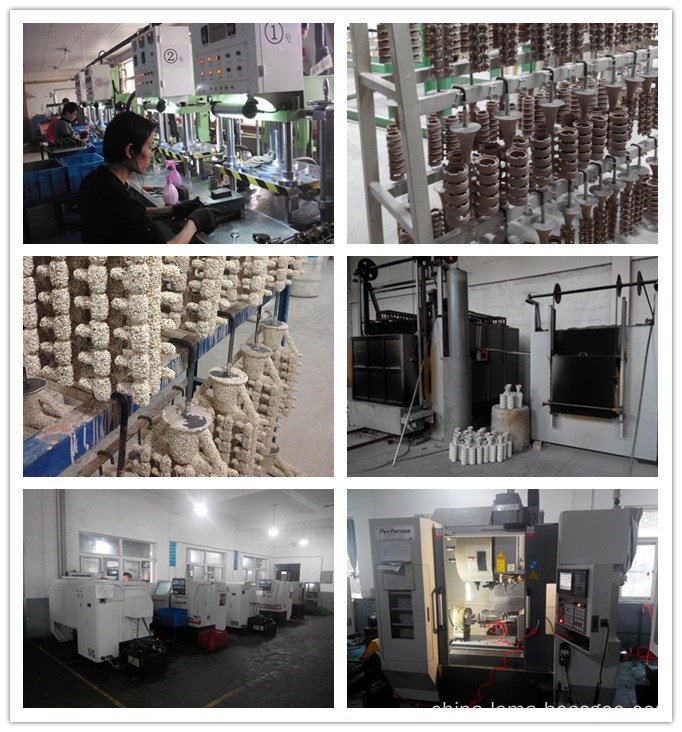
Steel Casting Part
Stainless Steel Lost Wax Casting, Steel Casting Part, Steel Investment Casting Part, Steel Silica Sol Casting Part
NINGBO BEILUN LEMA MACHINERY TECHNOLOGY CO.,LTD , http://www.china-lema.com